The threat of unplanned equipment failure in high-voltage operations is severe, driven by unseen contaminants in transformer oil that can trigger catastrophic losses. The Oil Breakdown Voltage (BDV) test is the most effective safeguard against this risk.
By directly measuring the oil’s dielectric integrity, the oil BDV test quantifies contamination from moisture and particles. This vital diagnostic is essential for preventing asset failure, upholding operational reliability, and ensuring safety across the power generation, industrial, and renewable energy sectors.
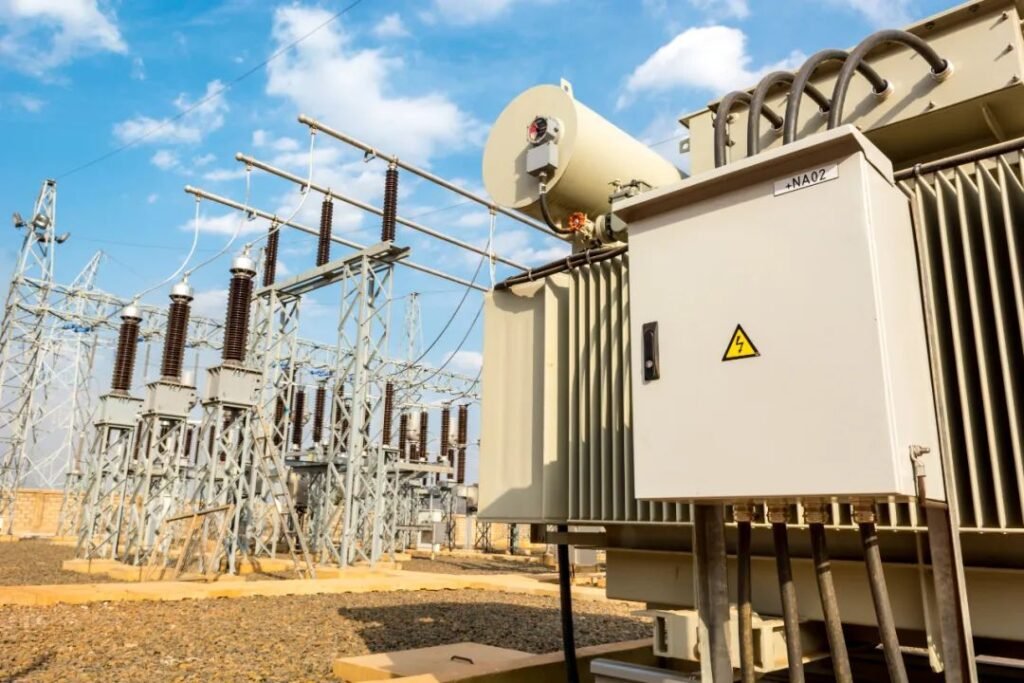
The oil within a transformer performs a dual role, but its most critical function is electrical insulation. This dielectric barrier is the primary defense for multi-million dollar assets, and its failure can lead directly to irreparable damage and operational collapse.
Given the high stakes, assessing the health of this insulating oil is a non-negotiable aspect of risk mitigation for any high-voltage operation. This principle applies universally, from large-scale power utilities and industrial plants to distributed renewable energy sites. Understanding the objective of this vital test is the first step toward securing these critical assets.
The Primary Objective and Diagnostic Value of the Oil BDV Test
The principal function of the Breakdown Voltage (BDV) test is to provide a quantitative measure of the dielectric strength of insulating oil. This assessment is critical for identifying latent vulnerabilities within high-voltage equipment.
Microscopic contaminants, particularly moisture and conductive particulates, can severely degrade the oil’s insulating properties, creating a precursor condition for catastrophic internal faults, such as arcing and complete equipment failure. The BDV test serves as the primary diagnostic tool to expose these otherwise undetectable risks.
The diagnostic power of the BDV test extends beyond a simple pass/fail determination; its true value lies in trend analysis. A consistent, downward trend in BDV readings is a leading indicator of progressive degradation, often signaling systemic issues like gasket leaks or the aging of cellulosic insulation. The test is exceptionally sensitive to two primary contaminants:
1.Emulsified Water: Under the influence of an intense electric field, polar water molecules suspended within the oil align to form low-impedance channels. This phenomenon facilitates a premature flashover at a voltage significantly below the specification for clean, dry oil.
2.Conductive Particulates: Solid contaminants, such as metallic fines from mechanical wear or carbon particles from minor thermal events, act as physical bridges across the insulating gap. These pathways effectively lower the voltage threshold required to initiate a dielectric breakdown.
Early detection of these deteriorating conditions through regular BDV testing enables proactive intervention and targeted maintenance, thereby mitigating the risk of an irreversible and costly asset failure.
Contaminant Type | Specific Examples | Mechanism of Failure |
Moisture (Water) | Leaking gaskets, atmospheric breathing | Lowers dielectric strength by forming conductive paths; accelerates aging of paper insulation. |
Conductive Particles | Metallic filings from wear, carbon from arcing | Reduces the effective gap between electrodes, creating localized high-stress points. |
Fibers (Cellulose) | Degradation of internal paper insulation | Absorbs moisture and forms conductive bridges that align with the electrical field. |
Dissolved Gases | Byproduct of overheating or corona | While not a direct cause of low BDV, its presence often correlates with particle-generating faults. |
The Role of Routine Oil Analysis in Preventing Unplanned Outages in Industrial Operations
In industrial manufacturing, operational continuity is paramount, and unplanned downtime
[1] can result in staggering financial losses. A primary, yet often overlooked, vulnerability is the health of on-site transformers that constitute the backbone of the facility’s power infrastructure.
Routine diagnostic testing of transformer oil provides the actionable intelligence necessary to mitigate the risk of a preventable power failure.
By systematically monitoring the dielectric integrity of transformer oil, maintenance teams can identify incipient faults caused by contaminants such as moisture or internal wear particulates. This early detection is the cornerstone of a transition from a reactive to a predictive maintenance paradigm.
For mission-critical facilities like data centers or semiconductor fabrication plants, where uninterrupted power is non-negotiable, the value of this approach is amplified. A declining trend in Breakdown Voltage (BDV) readings, for instance, serves as a clear, data-driven trigger for intervention. Rather than waiting for a failure or adhering to a rigid time-based service schedule, a maintenance manager can deploy targeted remedies.
A common example is scheduling an online oil purification system, which can restore the oil’s dielectric properties while the transformer remains energized and in service.
This predictive methodology transforms maintenance from a reactive, high-cost emergency function into a controlled, strategic process. It not only prevents catastrophic equipment failure and associated production losses but also optimizes maintenance expenditures and extends the operational lifespan of critical assets.
Maintenance Strategy | Decision-Making Process | Impact on Manufacturing Operations |
Reactive Maintenance | “Wait for it to fail.” No data is used. | Catastrophic. Triggers an emergency shutdown, massive production loss, and high repair costs. |
Preventive Maintenance | “Service every 12 months.” Based on a fixed schedule. | Better, but inefficient. Can miss early-stage faults and results in unnecessary, costly work. |
Predictive Maintenance (with BDV) | “Test quarterly and track the trend. Service when BDV drops by 15%.” | Optimal. Maximizes asset life, prevents unexpected downtime, and optimizes maintenance spending. |
Protecting High-Value Renewable Assets Through Strategic Oil Analysis
For operators of wind and solar farms, ensuring the reliability of high-value transformers is fundamental to protecting revenue streams and maximizing asset ROI. Routine analysis of insulating oil is a critical risk mitigation strategy tailored to the unique operational demands of the renewable energy sector.
Transformers in these applications—whether in wind turbines or solar plants—endure severe conditions that accelerate aging and increase the probability of premature failure. Key risk factors include:
Accelerated Thermal Wear: Caused by harmonic stress from power inverters.
Moisture Contamination: Driven by rapid load cycling inherent to renewable generation.
Environmental Corrosion: Especially prevalent in remote and offshore locations.
A transformer failure in a renewable setting leads to disproportionately high costs. Beyond the direct replacement expense, the true financial impact includes massive logistical hurdles and significant lost production revenue. This is particularly true for inaccessible assets, such as those in a wind turbine nacelle or on an offshore platform.
On-site oil testing provides the data-driven foresight needed to shift from reactive repairs to a proactive asset management strategy. By detecting early signs of insulation decay, it allows for planned, cost-effective interventions that prevent catastrophic failure. This proactive stance not only safeguards operational uptime and revenue but is also essential for meeting the stringent compliance requirements of insurers and equipment manufacturers.
Renewable Application | Specific Technical Stressor | How BDV Testing Mitigates Risk |
Wind Turbines (Step-up Transformer) | Constant vibration, thermal cycling, power electronic harmonics. | Detects early wear particles and moisture ingress from breathing cycles. |
Solar Farms (Inverter Transformer) | Rapid load changes (sun vs. cloud), high daytime temperatures. | Monitors accelerated oil aging due to severe thermal stress and potential for moisture ingress. |
Offshore Wind Farms | Corrosive salt-air environment, extreme inaccessibility. | Provides critical, on-site data to prevent catastrophic failures where repair is nearly impossible. |
The Strategic Imperative of BDV Testing in Mitigating Substation Failure Risk
In high-voltage substation management, forgoing routine Breakdown Voltage (BDV) testing on critical transformers is not a cost-saving measure but an acceptance of severe and unmitigated risk. The failure to monitor the dielectric integrity of insulating oil can directly lead to a catastrophic failure event with profound financial, operational, and regulatory consequences.
While the probability of such a failure may be low, its impact is exceptionally high. An internal arcing fault in degraded oil can trigger a violent tank rupture, effectively destroying a multi-million-dollar asset in seconds. However, the direct asset loss is often only the beginning of the financial fallout.
The cascading consequences include:
Extensive Capital Costs: Beyond replacing the primary asset, significant capital is required to repair or replace adjacent infrastructure damaged by the explosion and resulting fire.
Severe Operational Disruption: Unplanned outages lead to significant revenue loss, breach of service level agreements (SLAs), and potential instability across the wider electrical grid.
Substantial Liabilities and Penalties: The event triggers major liabilities, including the high cost of environmental cleanup, regulatory fines for service interruption and safety breaches, and potential legal action.
Extreme Safety and Reputational Risk: A catastrophic failure poses a grave risk to personnel safety and can cause lasting damage to the organization’s public and regulatory reputation.
The modest cost of a routine BDV test of oil is fundamentally a premium on an insurance policy against a high-impact, high-cost operational disaster. It represents a critical and non-negotiable component of responsible asset stewardship and enterprise risk management.
Consequence Category | Detailed Impact of a Major Transformer Failure |
Direct Financial Costs | Multi-million dollar asset replacement, extensive civil works, fire suppression, hazardous material cleanup. |
Operational & Grid Impact | Widespread blackouts, grid instability, long equipment lead times (12-24 months for large units). |
Regulatory & Legal | Severe government fines for service interruption, mandatory safety audits, potential lawsuits. |
Safety & Reputational | Extreme risk of injury or fatality to personnel, loss of public trust, negative media attention. |
Conclusion
Viewed correctly, the BDV test is your first line of defense against catastrophic failure. It is the single most effective action to protect high-value capital, eliminate unplanned downtime, and create a fundamentally safer operating environment.
[1]Learn about the financial and operational impacts of unplanned downtime in manufacturing.