Looking for Reliable Battery Testing Equipment Suppliers?
Finding the right battery testing equipment supplier can be tough. Poor choices lead to inaccurate results, wasted resources, and unreliable battery systems. You need a partner who understands your needs. A reliable battery testing equipment supplier offers high-quality, accurate instruments, comprehensive technical support, and after-sales service. They help ensure your batteries perform optimally and safely, like we strive to do at KV Hipot. Understanding what to look for is the first step. As a manufacturer, KV Hipot knows the challenges businesses face in sourcing dependable testing solutions. We’ve seen firsthand how the right equipment, backed by solid support, makes all the difference for clients like utility companies and project engineers. My experiences working with people like Muhammad, a Project Engineering Director in Saudi Arabia, and Spencer, a factory boss from the US, have shown me that product quality and reliable after-sales service are non-negotiable. They are often looking for performance comparable to European and American brands, and that’s the standard we aim for. Let’s explore what defines a good supplier and the equipment you’ll need.
What Equipment Do You Actually Need to Test Batteries?
Unsure which tools are essential for your battery testing needs? Investing in the wrong equipment can be a costly mistake and hinder your operations. We can clarify what’s important. Key equipment includes battery analyzers for capacity and internal resistance, load banks for discharge tests, specialized chargers/dischargers, and impedance testers. These tools provide a comprehensive view of battery condition.
Diving Deeper into Essential Battery Testing Equipment
When we talk about testing batteries, especially in critical industrial or utility settings, the right toolkit isn’t just beneficial; it’s fundamental. For someone like Muhammad, who is responsible for commissioning large-scale battery systems for power companies, having accurate and reliable equipment is paramount. He can’t afford guesswork.
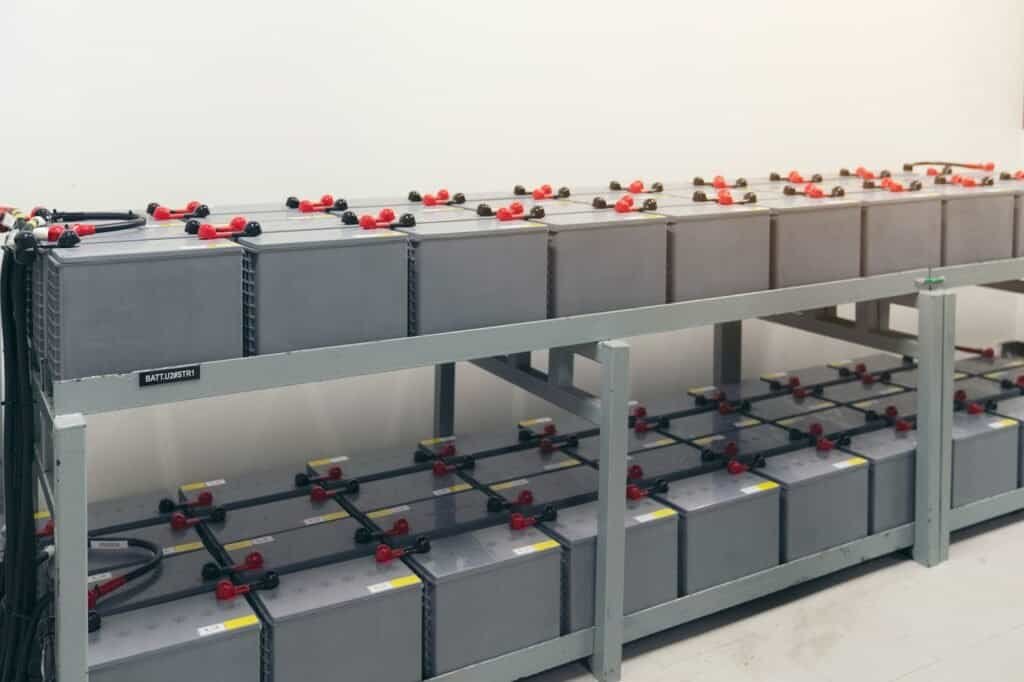
- Battery Capacity Testers/Discharge Load Banks: These are the workhorses. They don’t just tell you if a battery has charge; they tell you how much energy it can actually deliver. This is vital for acceptance testing – ensuring new batteries meet the manufacturer’s specifications – and for periodic maintenance to track degradation. Our KV Hipot load banks are designed for various discharge currents and voltages, offering flexibility.
- Internal Resistance/Impedance Testers: Think of these as a quick health check. A low internal resistance (IR) means the battery can deliver power efficiently. As batteries age or develop faults, their IR increases. Regularly tracking IR helps Muhammad identify weakening cells before they cause a system failure, addressing his pain point of low equipment reliability. These testers are often handheld and can be used online.
- Battery Charger Discharger Systems: These versatile units combine the functions of charging, discharging (capacity testing), and sometimes activation or conditioning. They are particularly useful for comprehensive battery bank maintenance and for reviving or assessing individual cells. For Spencer, who produces transformers that might integrate with battery backup systems, these systems can ensure the batteries supplied or integrated meet performance standards from the get-go.
- Battery Ground Fault Locators: In many industrial DC systems, batteries are ungrounded. A ground fault can be a serious safety hazard and can go undetected. This specialized equipment helps pinpoint the location of such faults quickly, ensuring system integrity and personnel safety, a key concern for any project director. The data from these tools is crucial. Many of our KV Hipot testers offer data logging and reporting, allowing engineers to maintain records, demonstrate compliance, and make informed maintenance decisions, directly combating the issue of unsupportable after-sales service by providing the tools for self-sufficiency and clear diagnostics.
Equipment Type | Primary Function | Key Benefit for Professionals like Muhammad & Spencer |
---|---|---|
Battery Capacity Tester | Measures actual Ah capacity under controlled discharge | Verifies performance against specs, crucial for project sign-off & factory QC. |
Internal Resistance Meter | Measures cell/battery impedance/resistance | Quick health indicator, predicts failure, essential for preventative maintenance. |
Battery Charger Discharger | Charges, discharges (capacity tests), activates, conditions | Comprehensive battery bank maintenance, cell revival, quality assurance. |
Load Bank | Simulates real-world load, tests discharge capability | Confirms battery can support critical loads during outages or peak demand. |
Ground Fault Locator | Detects insulation breakdown in ungrounded DC systems | Enhances operational safety and system reliability, prevents cascading failures. |
What Equipment Is Specifically Used to Check Battery Health?
Knowing a battery’s overall health is different from just its charge. Failing to accurately assess health can lead to unexpected system failures and costly downtime. What tools really pinpoint battery condition? To check battery health, specific equipment like internal resistance testers, impedance analyzers, capacity testers, and comprehensive battery charger discharger systems are used. These tools go beyond simple voltage checks to evaluate true performance capability. !
Diving Deeper into Battery Health Assessment Tools
Assessing true battery health is about understanding its ability to perform its designated function reliably over its expected lifespan. Surface-level indicators like voltage can be deceptive. A battery might show a healthy open-circuit voltage but falter under the slightest load if its internal health is compromised. For professionals like Muhammad, managing project engineering for power companies, or Spencer, ensuring the ex-factory quality of transformer systems that might rely on backup power, this distinction is critical. They need to avoid the pain point of low product performance and accuracy in their assessments. Key health assessment tools provide deeper insights:
- Internal Resistance (IR) / Impedance Testers: This is often the first line of defense in health assessment. IR is a measure of the opposition to current flow within the battery. A new, healthy battery will have a characteristic low IR. As it ages, undergoes charge-discharge cycles, or develops internal issues like corrosion or sulfation, the IR increases. Trending measurements over time helps identify degrading batteries. An increase of 25-50% from baseline often triggers further investigation. Our KV Hipot testers are designed for repeatability and accuracy.
- Capacity Testers (Load Banks): This is the most definitive health check, a “proof of performance” test. It measures the actual Ampere-hours (Ah) a battery can deliver under a specific discharge regime. It directly answers: “Can this battery support the critical load for the required duration?” For Spencer’s transformers or Muhammad’s utility backups, this is non-negotiable. A battery might have acceptable IR but still fail a capacity test if it has lost significant active material.
- Battery Charger Discharger Systems: These advanced systems play a crucial role in health assessment by allowing for controlled charge and discharge cycles. They can perform deep discharge tests to accurately determine capacity, followed by a precisely controlled recharge. Some units also offer features to “activate” or “recondition” batteries that may have lost some capacity due to sulfation or imbalance, potentially extending their usable life. For Muhammad, this means being able to rigorously test battery banks and even attempt to restore performance, while for Spencer, it allows for detailed quality control of battery components integrated into their systems. These systems often provide detailed reports on the entire charge/discharge cycle, offering valuable data on battery behavior and health. Using these tools in concert, rather than in isolation, provides a holistic view. For example, high IR might prompt a capacity test using a load bank or a full cycle test with a charger discharger to confirm the extent of degradation. This comprehensive approach is what we advocate at KV Hipot, supporting it with robust equipment and technical guidance.
What Are the Most Common Battery Testing Methods?
Many methods exist to test batteries, but which are most effective? Using inappropriate methods can give false confidence or miss developing problems, leading to system failures when they’re needed most. Common battery testing methods include capacity testing (discharge testing), internal resistance/impedance measurement, voltage checks, and using integrated battery charger discharger systems for comprehensive cycling and analysis.

Diving Deeper into Common Battery Testing Methods
For businesses that depend on battery reliability – from utility companies ensuring grid stability, like those Muhammad services, to manufacturers like Spencer who need to guarantee their equipment integrates with dependable power sources – understanding and correctly applying common testing methods is crucial. It’s not just about having the equipment; it’s about using it effectively to gather actionable data.
- Capacity Testing (Discharge Testing): This remains the most conclusive method to determine a battery’s true ability to perform. The test involves discharging a fully charged battery at a constant current (or power/resistance) until it reaches a specified end-of-discharge voltage. The duration it sustains this discharge gives its actual capacity. The “C-rate” is critical. While thorough, it’s also time-consuming. Our KV Hipot capacity testers allow for precise control and automated data logging.
- Internal Resistance/Impedance Measurement: This is a much quicker, non-intrusive method. A small AC signal is injected, and the resulting voltage drop is measured. It’s excellent for identifying problematic cells within a string and for trending degradation over time, often without taking the battery offline. An increase in IR of 25-30% over baseline usually warrants further investigation. This method directly addresses the pain point of unexpected equipment failure by providing early warnings.
- Voltage Measurement (with context):
- Open Circuit Voltage (OCV): Gives a rough state of charge but reveals little about health.
- Float Voltage (for standby systems): Crucial for batteries on continuous charge. Incorrect float voltage can damage batteries.
- Voltage Under Load: Observing voltage drop when a load is applied can indicate high internal resistance or insufficient capacity.
- Battery Charger Discharger Cycling: This method involves using an integrated system to perform one or more complete charge and discharge cycles. This is more than just a simple capacity test; it allows for observation of the battery’s behavior throughout the entire process. Parameters like charge acceptance, discharge characteristics at various rates, and efficiency can be evaluated. For someone like Spencer, this can be used to qualify new battery batches or designs for his transformer products. Muhammad can use these systems for detailed commissioning tests on new battery banks or for in-depth troubleshooting of problematic strings, as these units often log extensive data throughout the cycles. This offers a very comprehensive view of battery health and performance capabilities. A robust battery maintenance program, like those we help our clients establish, typically combines these methods. For instance, regular IR and voltage checks, with periodic capacity tests or full cycling tests for critical systems. This comprehensive approach, supported by reliable KV Hipot equipment, minimizes the risk of sudden failures.
Conclusion
Selecting the right battery testing equipment and suppliers is vital. It ensures accurate assessments, reliable battery performance, and supports the longevity of your critical power systems. KV Hipot is committed to providing top-quality solutions.